

Choose the proper directory and proper file and click on List Files Type button in which you should has to mention the file type I. In the same dialogue box, you will see two side boxes side by side showing the File and Directories.Then another dialogue box opens where you need to browse for that file which you are going to import into ANSYS.Click on ANSYS Icon and it opens a new dialogue box named ANSYS Multiphysics Utility Menu.
ANSYS TUTORIAL SOFTWARE
ANSYS TUTORIAL HOW TO
How to convert a Wire frame model into Solid model in ANSYS Explanation:Ī step by step procedure is to be adopted to understand how a model is analyzed by importing and how can we convert that wireframe model into a solid model and is as follows. In this article, I will be explaining to you about How to convert a Wireframe model into the Solid model in ANSYS software in a detailed manner. If you want to analyze apart under the application of loads, then you should have to import that model into ANSYS software in the form of Parasolid format or any other format. Therefore, this is the complete explanation of converting areas into nodes in ANSYS software.Ĭonversion of Wireframe model into the Solid model in ANSYS
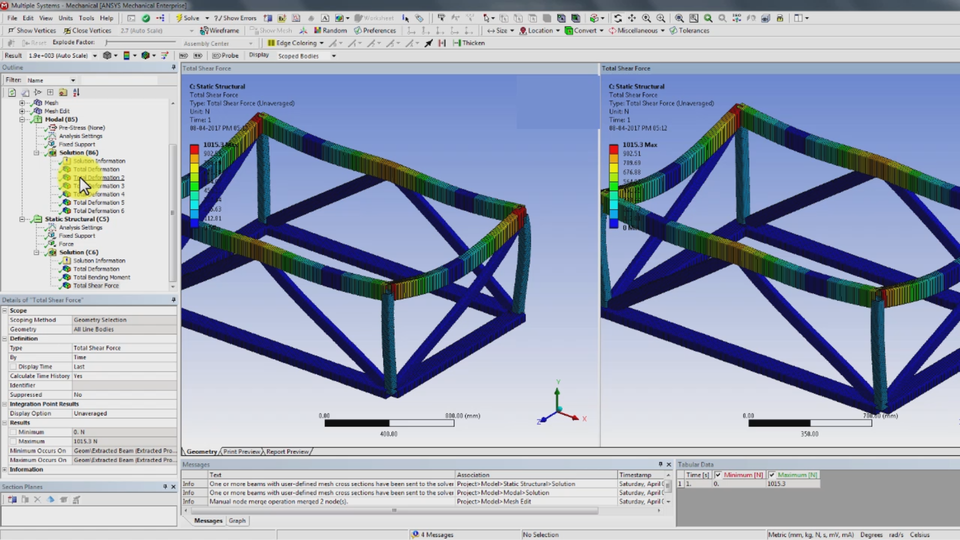
If automatic renumbering is disabled, you must ensure that the element/node numbering is unique for each mesh.
ANSYS TUTORIAL MANUAL
For every analysis system (mesh), you have the choice between automatic renumbering (default) and manual configuration. Meshes from upstream to downstream Mechanical Models are renumbered automatically to avoid any overlap. Mechanical does not allow overlap of node/element number from multiple systems therefore, the import fails if the meshes from different systems are overlapping in node/element numbers. It is possible to combine composite shell, composite solid, and non-layered shell and solid meshes to perform mixed analysis.

Meshes can be imported into Mechanical from multiple systems.

In the next step, we are going to model two metal parts and then at the end we will combine models into static structural. In this tutorial, first we are going to model specimen geometry in CAD software then we will apply composite layers in ACP tools. The results from the test are commonly used to select a material for an application, for quality control, and to predict how a material will react under other types of forces. Tensile testing, is also known as tension testing is a fundamental materials science test in which a sample is subjected to a controlled tension until failure.
